What you need, when you need it
We’re committed to ensuring you get what you need, when you need it. This is why we keep more than 20,000 products in stock and continue to develop our stock management processes and systems to actively manage our stock levels.
Brexit
We do everything we can to ensure that stock is available to our customers, no matter what.
For Brexit we:
- Secured additional storage facilities
- Over-stocked our fastest moving catalogue and customers’ business-critical products
- Worked with our supply chain to mitigate pricing and supply chain risks
- Obtained an EORI number from HMRC ensuring a smoother importation process for EU products.
- Updated EU supplier lead times in product management software to increase stockholding to allow for longer lead times.
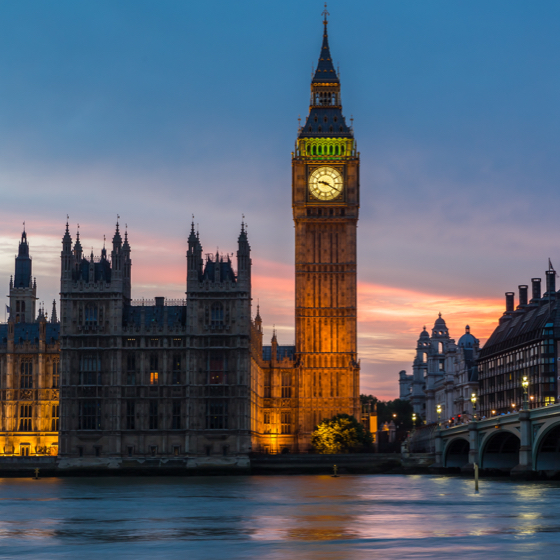
Driver shortage
To mitigate the impact of the ongoing lorry driver shortages and rising cost of freight we:
- Implemented of a new process to allow mass forecast changes to combat consumption fluctuations due to driver shortages (including those caused by COVID-19 lockdowns and restrictions)
- Conducted weekly meetings with Planning and the Product & Services team to review supplier service levels and costs
- Used our own fleet of vans to back-haul products from suppliers
- Built internal business insight tools with Mintec to analyse 14,000 raw material commodities, shipping costs and exchange rate movements daily, ensuring that if a product moves in the market, we challenge our supply chain using factual raw material data.
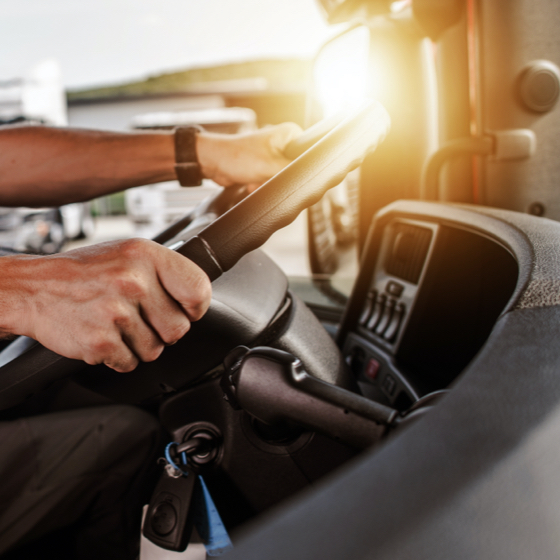
COVID-19 pandemic and lockdowns
During the COVID-19 outbreak, subsequent lockdowns and continued disruption, we:
- Quickly reacted to the surge in demand and the risk of rogue products flooding the marketplace by adding two Procurement heads to the already established PPE team. Their job was to focus on sourcing Disposable Covid-19 related products.
- Widened our supply chains while ensuring strong due diligence to verify that all certifications and products were from a sustainable and legitimate supply chain (in line with our BSIF membership).
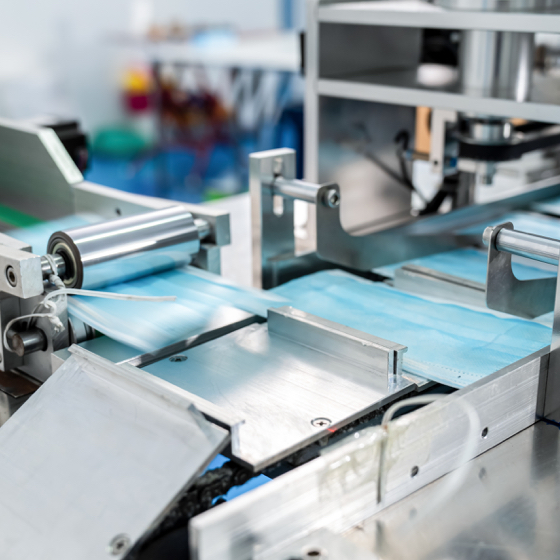